Introduction
In the wire manufacturing industry, surface treatment is crucial for improving product quality and process efficiency. The In-Line Borax Coating Machine has emerged as an essential solution, providing a seamless, automated way to apply borax-based lubricants to wire rods before drawing. This technology ensures smoother operations, extended die life, and superior finished products.
In this blog, we’ll explore how an In-Line Borax Coating Machine works, its benefits, and why it’s a game-changer for wire production.
What Is an In-Line Borax Coating Machine?
An In-Line Borax Coating Machine is an automated system that applies a thin, uniform layer of borax (sodium borate) lubricant to metal wires before the drawing process. This coating reduces friction, prevents oxidation, and enhances wire ductility.
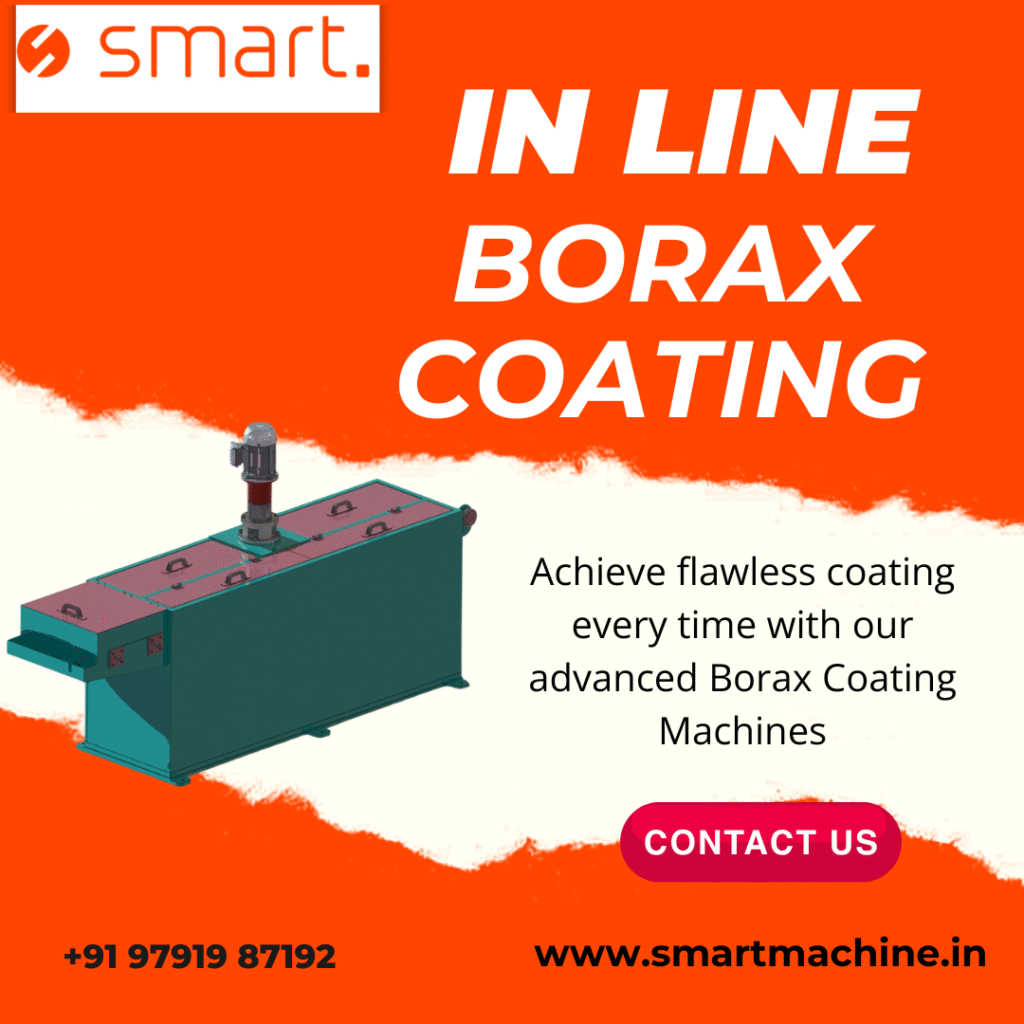
Key Components:
- Pre-treatment Cleaning Unit – Removes rust, scale, and contaminants.
- Borax Application Chamber – Evenly coats the wire with borax solution.
- Drying System – Ensures proper adhesion before drawing.
- Control Panel – Adjusts coating thickness and speed for precision.
Why Use Borax Coating in Wire Drawing?
Borax coating offers several advantages:
1. Reduces Friction & Wear
- Minimizes die abrasion, extending tool life.
- Lowers drawing force, saving energy.
2. Improves Surface Finish
- Prevents scratches and surface defects.
- Ensures smooth, consistent wire output.
3. Enhances Lubrication Efficiency
- Works well with both dry and wet drawing processes.
- Compatible with various metals (steel, copper, aluminum).
4. Cost-Effective & Eco-Friendly
- Reduces the need for additional lubricants.
- Non-toxic and easy to clean.
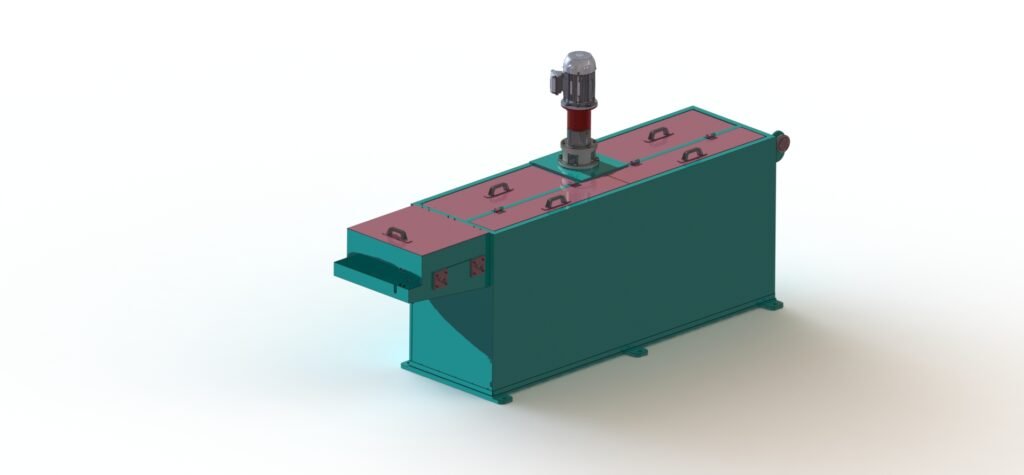
How Does an In-Line Borax Coating Machine Work?
The process involves three key stages:
- Pre-Cleaning – The wire passes through a descaling or pickling unit to remove impurities.
- Borax Application – The wire is submerged or sprayed with a borax solution.
- Drying/Curing – Excess moisture is evaporated, leaving a dry, adherent coating.
Since the machine operates in-line, it integrates smoothly with existing wire drawing setups, minimizing downtime.
Industries That Benefit from Borax Coating Machines
- Wire & Cable Manufacturing (electrical, automotive, construction wires)
- Fastener Production (bolts, screws, nails)
- Spring & Wire Forming (precision components)
- Metalworking & Forging (pre-treatment for further processing)
Choosing the Right In-Line Borax Coating Machine
When selecting a machine, consider:
✔ Coating Uniformity – Ensures consistent lubricant application.
✔ Automation Level – Reduces manual intervention.
✔ Compatibility – Works with your wire material and diameter.
✔ Energy Efficiency – Low power consumption and minimal waste.
Conclusion
An In-Line Borax Coating Machine is a smart investment for wire manufacturers looking to improve efficiency, reduce costs, and enhance product quality. By integrating this technology into your production line, you can achieve smoother wire drawing, longer die life, and superior end products.
Interested in optimizing your wire drawing process? Explore our high-performance In-Line Borax Coating Machines today!