Introduction
High-quality welding wire is essential for strong, consistent welds in industrial applications. However, manufacturers often face challenges like surface defects, inconsistent diameters, and premature wire breakage. A wet drawing machine provides an effective solution by enhancing wire quality through advanced lubrication and cooling.
In this blog, we’ll explore common welding wire problems and how wet drawing machines help overcome them while improving efficiency and reducing costs.
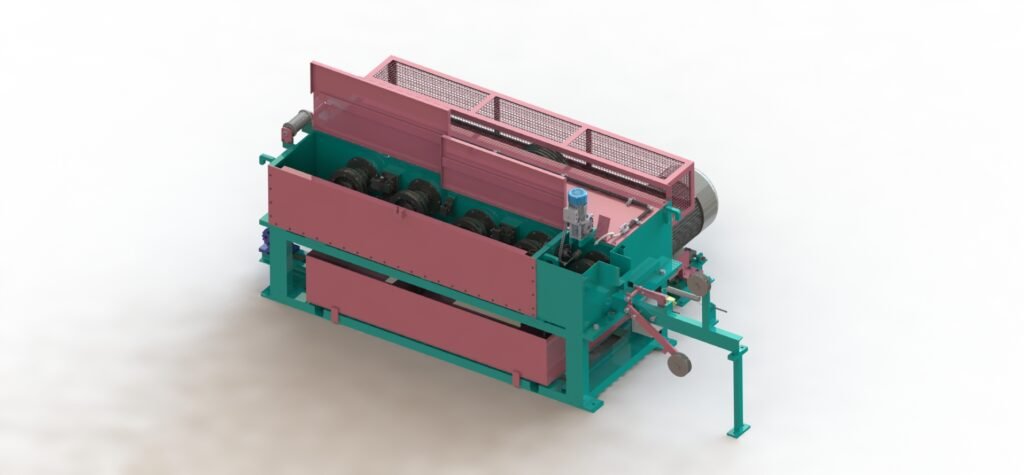
Common Welding Wire Problems & How a Wet Drawing Machine Solves Them
1. Surface Defects (Scratches, Cracks, or Oxidation)
Problem: Dry drawing creates friction, leading to scratches, cracks, and oxide buildup on the wire surface.
Solution with :
- Uses a lubricant-coolant mixture to minimize friction.
- Produces a smoother, defect-free surface, ideal for high-performance welding.
2. Inconsistent Wire Diameter
Problem: Variations in wire thickness cause poor arc stability and weak welds.
Solution with Wet Drawing Machine:
- Ensures precise dimensional control for uniform diameter.
- Critical for automated welding processes requiring consistency.
3. Excessive Wire Breakage During Drawing or Welding
Problem: Brittle wire due to excessive friction and heat leads to breakage.
Solution with Wet Drawing Machine:
- The cooling effect prevents overheating, improving ductility.
- Reduces internal stresses, resulting in stronger, more flexible wire.
4. Short Die Life & High Maintenance Costs
Problem: Dry drawing wears out dies quickly due to heat and friction.
Solution with Wet Drawing Machine:
- Lubrication reduces abrasive wear, extending die lifespan by 30-50%.
- Lowers operational costs with fewer replacements.
5. Poor Tensile Strength & Workability
Problem: Improper drawing weakens the wire, causing deformation.
Solution with Wet Drawing Machine:
- Enhances mechanical properties for higher tensile strength.
- Ensures better elongation and durability.
How a Wet Drawing Machine Works to Improve Welding Wire Quality
A wet drawing machine submerges the wire in a lubricant-coolant mixture while pulling it through dies. This process:
✔ Reduces friction for a smoother surface finish
✔ Maintains consistent temperature to prevent overheating
✔ Improves wire strength and flexibility
✔ Extends die life for cost savings
Key Benefits of Using a Wet Drawing Machine for Welding Wire
- Higher-quality wire with fewer defects
- Reduced breakage for less material waste
- Longer die life for lower maintenance costs
- Faster production speeds without sacrificing precision
- Energy-efficient compared to dry drawing
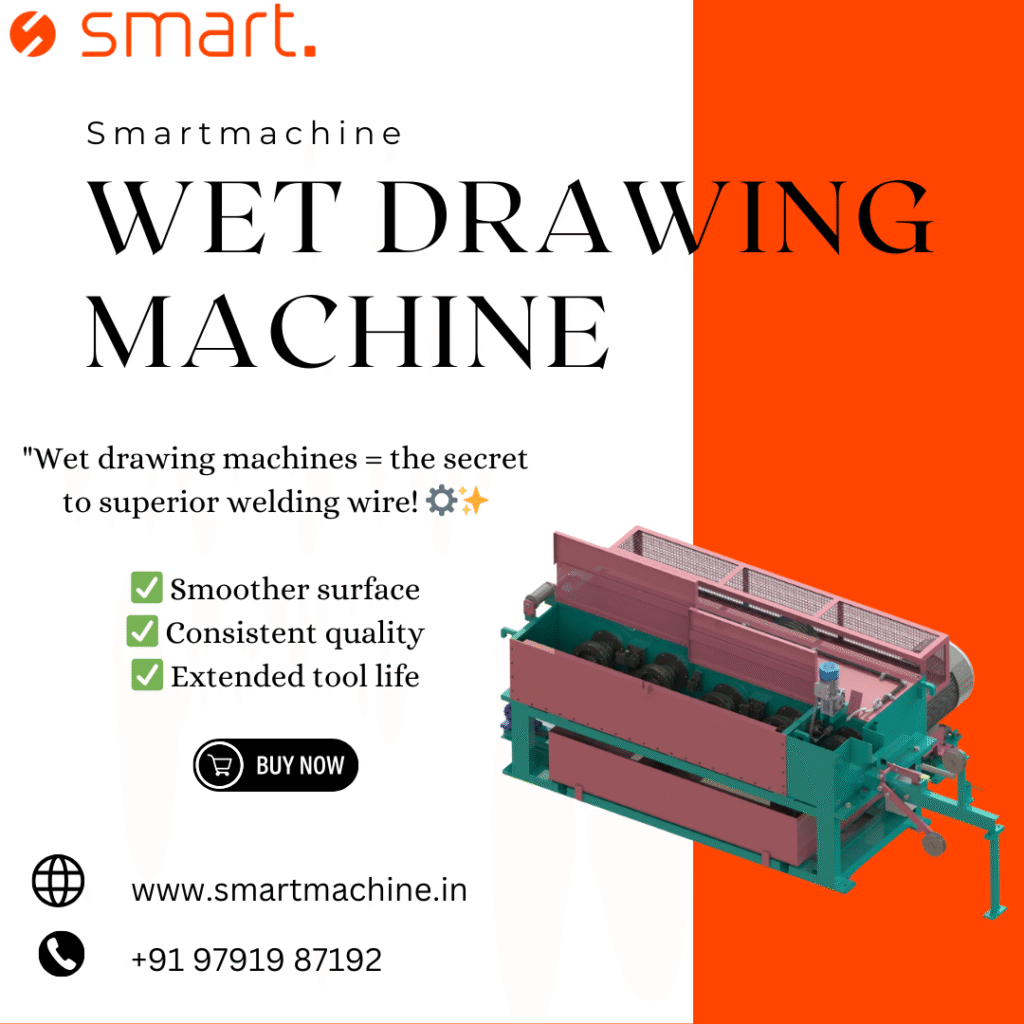
Conclusion
A wet drawing machine is a game-changer for welding wire production, solving common issues like surface defects, inconsistent diameters, and breakage. By integrating this technology, manufacturers can achieve:
✅ Better weld quality
✅ Lower production costs
✅ Increased efficiency
Upgrade your wire production today!
📞 Contact us to find the best wet drawing machine for your welding wire needs.